Light Weight Aluminum Spreading Proficiency: Strategies and Devices for Remarkable Outcomes
Understanding the art of light weight aluminum casting calls for a fragile balance of accuracy, technique, and the use of specialized devices. As we explore the detailed methods and tools included in light weight aluminum spreading proficiency, one can not neglect the value of sophisticated pouring and cooling methods that can boost the final end result.

Value of Proper Melting Methods
Using exact temperature level control throughout the melting procedure is extremely important in making sure the top quality and honesty of light weight aluminum spreadings. The melting of aluminum is a vital step in the spreading process, as it directly impacts the final buildings of the casted components. Correct melting methods are crucial to attain the wanted metallurgical framework, mechanical residential or commercial properties, and surface finish of the aluminum parts.
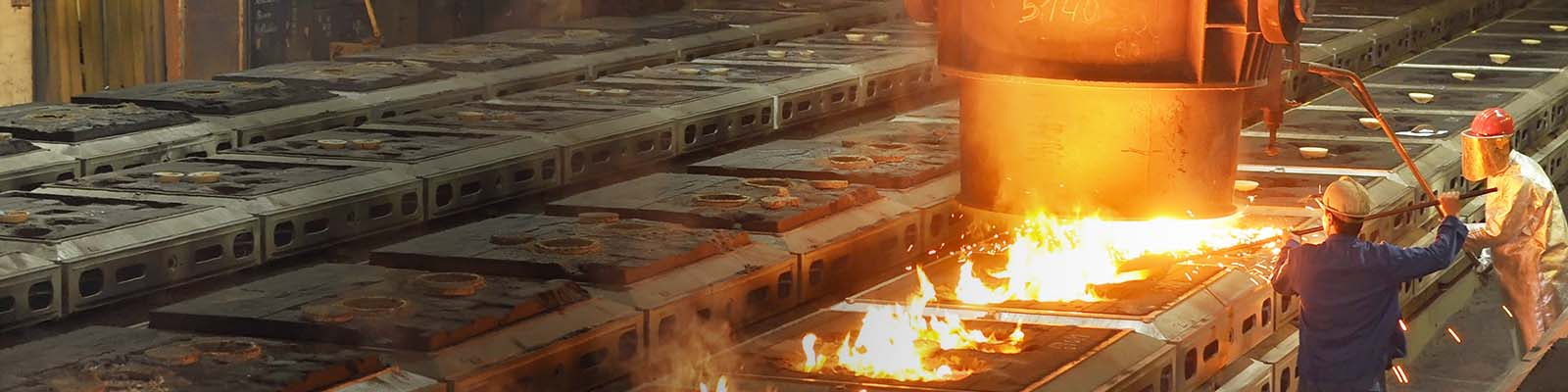
Additionally, tracking and changing the thaw temperature level throughout the procedure assistance stop getting too hot, which can create grain development and influence the total top quality of the light weight aluminum spreading. Following specific melting strategies not just boosts the quality of the end product however likewise enhances the effectiveness and cost-effectiveness of the casting process.
Crucial Mold Preparation Tips
Correct prep work of mold and mildews is a basic aspect in the aluminum spreading procedure, making certain the effective replication of complex information and measurements in the last casted elements. The important mold preparation actions begin with selecting the appropriate molding product, such as sand or financial investment casting materials, based on the intricacy of the component and preferred surface. Prior to pouring the molten aluminum, the mold and mildew tooth cavity should be carefully cleaned and dried to avoid defects in the spreading. Furthermore, applying mold and mildew layers can aid boost surface finish and lengthen mold life.
Moreover, proper gating and risering layout are important in mold and mildew preparation to ensure audio castings with very little issues like porosity and shrinking. Eviction system helps with the flow of molten steel into the mold dental caries, while risers help stop shrinkage by giving additional molten steel as the casting solidifies. Mindful consideration of these facets throughout mold preparation dramatically contributes to the high quality and honesty of the final light weight aluminum cast parts.
Advanced Pouring and Cooling Techniques
Carrying out innovative pouring and cooling down approaches is critical in enhancing the light weight aluminum spreading procedure for improved performance and top quality outcomes. Utilizing methods such as vacuum cleaner spreading can dramatically decrease porosity in the final product, causing boosted mechanical residential or commercial properties. By evacuating see this here the air from the mold dental caries prior to putting, the threat of gas entrapment is decreased, causing a denser and even more structurally sound casting.
Additionally, utilizing controlled cooling methods, such as water quenching or air cooling, can influence the material's microstructure and mechanical attributes (about aluminum casting). Fast cooling can assist achieve finer grain frameworks and boosted mechanical properties, making the cast aluminum preferable for applications calling for high stamina and toughness
In enhancement, executing directional solidification techniques, where the spreading solidifies progressively from one end to click to find out more an additional, can help minimize internal defects and boost overall component integrity. By carefully taking care of the temperature differentials throughout solidification, the development of shrinkage porosity and warm tears can be minimized, bring about higher quality spreadings with improved mechanical efficiency.
Important Devices for Aluminum Spreading
Enhancing the efficiency and top quality outcomes of aluminum casting procedures counts greatly on the application of particular devices made to optimize different elements of the spreading operation. One necessary device for aluminum casting is the crucible.
Another vital tool is the mold and mildew. Mold and mildews can be made from products like sand, metal, or plaster and are used to shape the molten aluminum into the desired type. about aluminum casting. Correct mold design and materials are crucial for accomplishing exact spreading measurements and surface area coatings
In enhancement to crucibles and molds, a heater is a fundamental device for aluminum casting. Heating systems heat the metal to its melting point, guaranteeing it remains in a state all set for spreading. Crucial for maintaining consistent temperature levels and ensuring the light weight aluminum continues to be liquified, heaters are readily available in numerous kinds, such as electric, gas, or induction furnaces, each with its advantages for details casting requirements.
Ending Up Touches and High Quality Checks
Upon completing the casting procedure, thorough interest to finishing touches and strenuous high quality checks is critical to ensure the honesty and accuracy of the aluminum parts - about aluminum casting. Ending up touches involve the removal of any kind of excess material, such as flash, gating systems, or rough sides, to accomplish the desired final form and surface area high quality. This step commonly consists of procedures like grinding, sanding, or fired blasting to refine the appearance and appearance of the actors parts
Quality checks are then conducted to confirm that the elements meet the specified requirements and criteria. These checks might involve dimensional examinations using accuracy devices like calipers or coordinate measuring machines to make sure accuracy. Furthermore, non-destructive screening techniques such as ultrasonic screening or X-ray evaluation can be employed to detect any internal flaws that click here for more info may compromise the architectural stability of the components.
Verdict
To conclude, mastering light weight aluminum spreading methods and making use of the right tools is essential for accomplishing extraordinary outcomes. Correct melting techniques, mold prep work, pouring and cooling down techniques, in addition to finishing touches and quality checks are vital steps in the spreading procedure. By complying with these actions very carefully and making use of the ideal tools, one can ensure a premium and effective light weight aluminum spreading production.
As we explore the detailed strategies and devices involved in light weight aluminum casting mastery, one can not neglect the significance of advanced pouring and cooling down techniques that can elevate the last outcome.Appropriate prep work of molds is a basic facet in the light weight aluminum casting procedure, guaranteeing the effective replication of elaborate details and measurements in the final casted parts. Prior to pouring the liquified aluminum, the mold and mildew dental caries need to be carefully cleaned up and dried out to stop issues in the spreading.Enhancing the effectiveness and top quality end results of aluminum spreading processes counts heavily on the utilization of details devices designed to maximize various aspects of the casting procedure.In enhancement to molds and crucibles, a heater is a fundamental device for aluminum spreading.